Any organization looking at repairing or replacing equipment can be turned off by the price tag or how time-consuming these processes can be. When a critical piece of equipment fails, the expense of repairs doesn’t stop at the machine. The cost also takes into consideration the downtime of that machine. The cold spray coating process can significantly reduce or maybe even eliminate downtime and provide several other benefits to organizations.
This blog post will cover the six benefits of choosing cold spray over other repair methods. These benefits are:
- Physics and structure
- Portability
- Speed
- No Melting
- Thicker Coatings
- Decreased Surface Prep
For more information like this and all of the latest industry news on the cold spray coating process, request more information from ColdSpray.com.
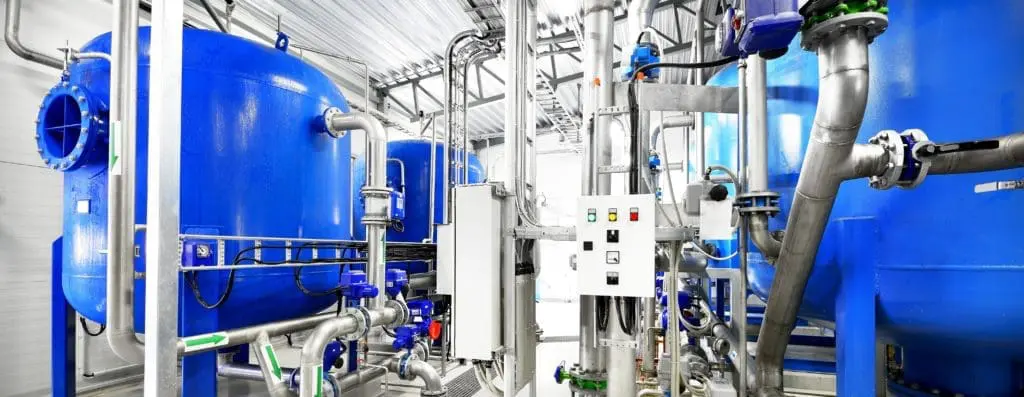
New(ish) & Newsworthy
The cold spray coating process was first invented in the mid-1980s at the renowned Russian Academy of Sciences. However, it wasn’t until the late-1990s that it was first patented in the United States. At that point, it began to intrigue aerospace companies, national labs, and the Department of Defense. Fast forward to today, and after more than twenty years of research and development, the cold spray coating process is solving real-world problems every day.
The cold spray coating process combines metal particles with a high-pressure gas jet. The gas jet accelerates these metal particles to supersonic speeds through a nozzle and onto a substrate’s surface. The metal particles bond to the desired substrate without the chemical and molecular changes that accompany high-temperature spray and coating applications.
To sum up, the cold spray coating process offers several advantages for equipment repair. An organization can lengthen equipment life, reduce downtime, save money on new purchases, and reduce labor costs attached to repairs.
Using The Cold Spray Coating Process To Your Company’s Advantage
Unlike high-temp spray and coating applications, the cold spray coating process does not change the substrate. During the cold spray process, the materials remain in a solid state. This differs from the physical changes that can occur with high heat, such as melting.
As a result, the sprayed metal equipment experiences reduced oxidation. The surface oxides are blasted away by the impacting metal particles, which also assists with the bonding process. Further, the bonded segment does not experience post-application shrinkage from solidification, as materials do during other high-temperature thermal spray or traditional welding applications.
Due to the extremely high pressure applied to the spray coating and the velocity achieved exiting the cold spray nozzle, the sprayed metal particles bond like Play-Doh thrown at the substrate surface.
A molecular embrace like this is difficult to break. It’s essentially a combination of metallurgical and mechanical bonding. Meaning, the cold spray coating is many times indistinguishable from the substrate. The precision of the cold spray particles exiting the “gun” in a narrow “beam” affords greater accuracy in the application. It offers more coating thickness options and shape control than any thermal spray method.
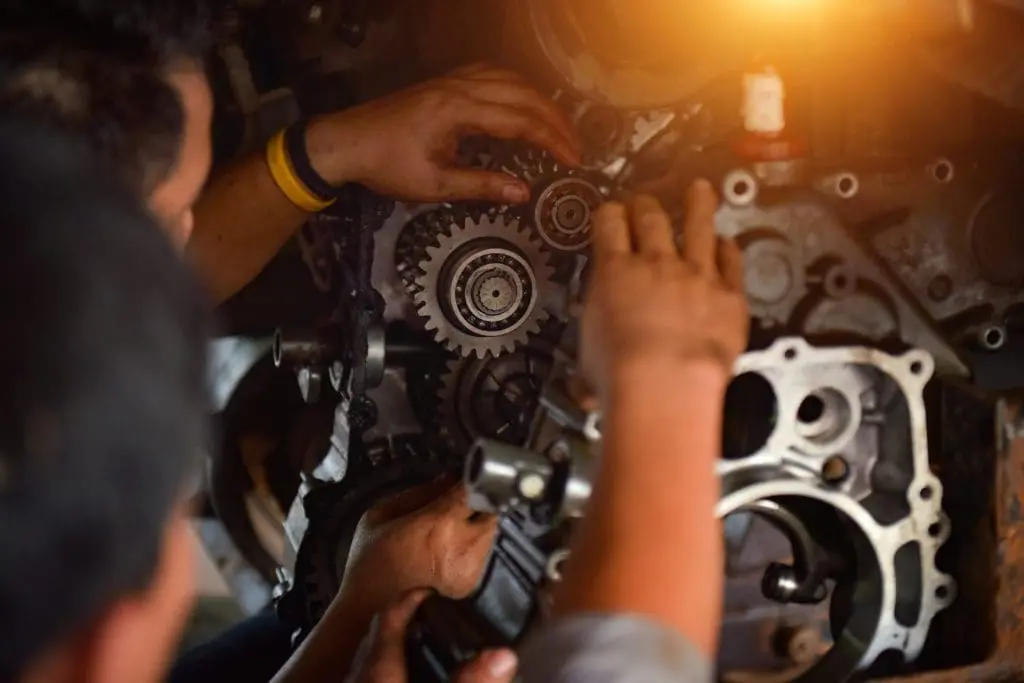
What Are The Best Metals For Spray Coatings & Substrates?
The best metals for coatings include:
- Aluminum
- Copper
- Stainless Steel
- Titanium
- Alloys of the above materials
The best surfaces for the cold spray coating process include any surface that can withstand the high-pressure cold spray coating process. Any soft substrate would likely erode under the pressure of the spray. The same would be true for friable surfaces.
Industrial Relevance
To date, cold spray coatings are commonly used in:
- Aerospace: in aluminum coatings to refurbish or protect magnesium components
- Cookware: ferrite coatings on certain conduction cookware pieces
- Free Forms
- Heavy Industrial: in shafts and cast iron engine casings
- Near Net Shapes
- Nuclear Industry: fuel rod coatings and component repairs
- Performance-Enhancing Layers
- Turbine Component Coatings
- And many more…
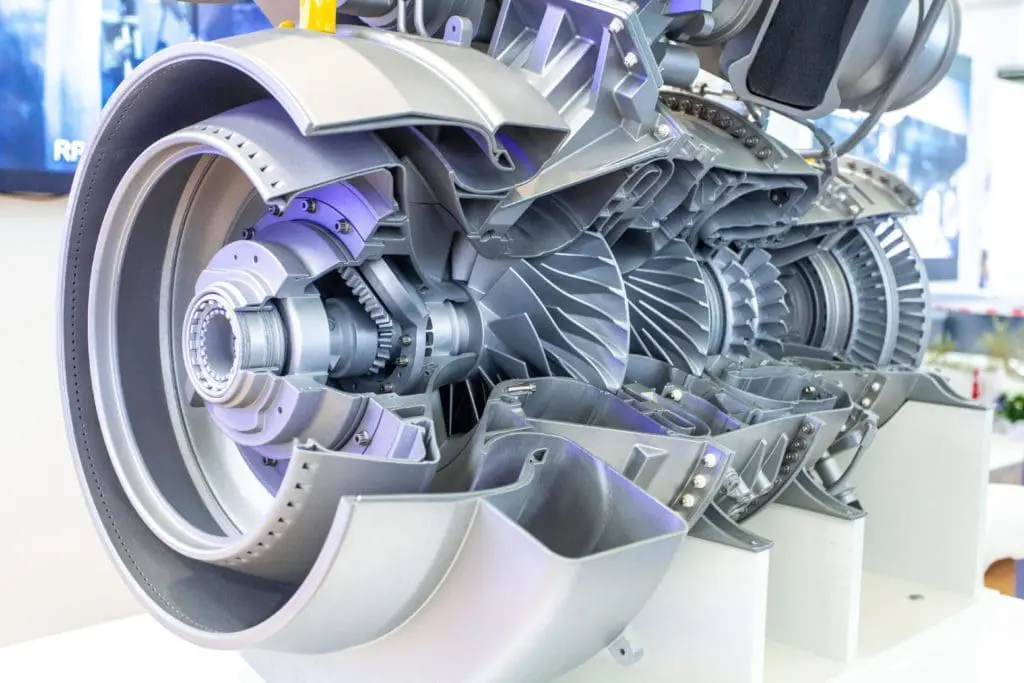
The Cold Spray Coating Process Advantages
We already covered the physics and structure of cold spray bonds, which can preserve both the spray particles and the substrate’s metal composition and bond size.
In addition to this, there are five additional advantages we want to cover:
- Portability: Cold spray technology may reduce or eliminate the need to pull machinery or disassemble equipment to access the surface area that needs to be repaired or coated. Cold spray guns are incredibly agile. They’re designed to fit into a variety of spaces to apply reliable bonds and precise coatings.
- Speed: Because cold spray technology eliminates several steps from a conventional high-temp bonding process, repairs happen in a fraction of the time. There’s no need for “cooling.” You can often achieve a “shoot-and-start-up” result with a cold spray repair.
- No Melting: Because of cold spray’s high-pressure bond, melted metals are unnecessary, nor are they a by-product.
- Thicker Coatings: With no worry over solidification stress, you can thicken the coating at a lower risk.
- Decreased Surface Prep: Cold spray’s coating process often reduces the substrate’s need to be grit blasted. Because of cold spray’s narrow particulate stream, you may also reduce or eliminate the need for masking.
Cold spray technology doesn’t compromise the particle or substrate structure during the bonding process, cold spray bonds, coatings, and repairs last longer than those from welding or thermal spray applications.
When your company’s equipment lasts longer, you save money over time with reduced capital expenditures on machinery.
Plus, your production line or other machinery can enjoy more “up” time during the life of your equipment.
What does all of this mean? More revenue potential with fewer operational interruptions.
With cold spray’s agility, you may also save significantly on labor. Your maintenance staff can pinpoint the problem part and fix it with increased skill and speed.
For all of the latest industry news on the cold spray coating process, request more information from ColdSpray.com.