Cold Spray has become a major part of multiple manufacturing industries, including aerospace, marine, and defense. It provides many benefits over traditional welding processes. One of the most significant advantages is that the cold spray process does not create heat affected zones. This is because Cold Spray has a significantly lower spray temperature than the material’s melting point. You may be asking yourself, what is a heat affected zone and why is it important? Let’s find out.
What Is The Heat Affected Zone (HAZ)?
When the term heat affected zone is mentioned, it is typically being referred to in the welding industry. The heat affected zone is the area on any metal that has not been melted but has undergone property changes due to the exposure to the high temperatures during the welding process. Typically, the HAZ can be found between the weld and untouched metal as seen below.
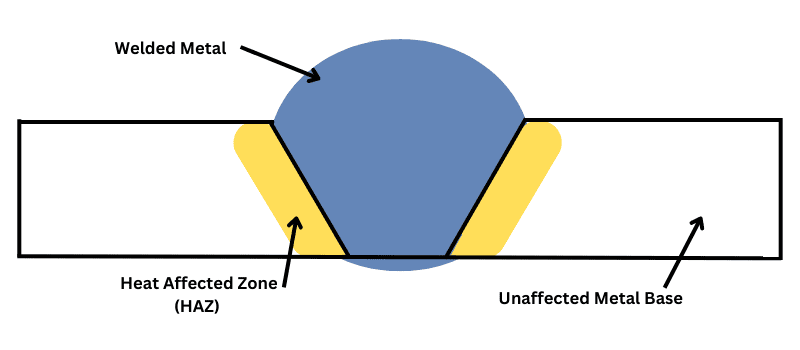
The size of the heat affected zone varies by project because it is determined by the amount of heat going into the material. The HAZ is also affected by the thermal diffusivity of the material being worked on. The higher the thermal diffusivity, the faster the heat transfer, which means the material cools quicker, the resulting effect is that the HAZ width is significantly reduced compared to a material with lower thermal diffusivity.
Why Is HAZ So Important?
Remember, when you are welding you are temporarily changing the properties of the material you are working on. These changes in the structure and properties of your material can create various issues and challenges if not done correctly. The main issue with welding and HAZ is that the HAZ often differs from the base material, typically resulting in lower/higher strength, cracking, reduced corrosion resistance or lower toughness. Due to all these changes, the HAZ is often the point where failures occurs.
In some materials, the HAZ can end up being stronger than the base material where in others it may be softer and weaker than the base material. Both results pose major challenges for the design, function and trustworthiness of the material. The process of welding unfortunately always bears the possibility of a HAZ that could fail. However, Cold Spray Manufacturing does not create a HAZ on any materials, unlike traditional welding.
What Is Cold Spray?
Cold Spray, also referred to as supersonic particle deposition, is a high-energy solid-state coating and powder consolidation process. During the cold spray process, micro-sized metal powder particles are accelerated supersonically towards a substrate. The impact results in significant plastic deformation, mechanical interlocking, and metallurgical bonding of the particles to the substrate and/or previously deposited layers of particles. The metal powder particles never reach melting temperatures, avoiding unwanted thermal effects, but are bonded through kinetic energy transfer and adiabatic shear minimizing substrate heating, and maintaining dimensional stability as well as the materials’ microstructure.
Cold spray deposited metals exhibit low porosity (< 1%), exceptional mechanical tensile strength (> 60 ksi) and adhesion (> 10 ksi), with fine grain structure and microstructures that can generally be maintained from the powdered state to the as-deposited condition. Another benefit of cold spray is that it produces a high density, high hardness, and cold-worked microstructure with compressive residual stresses, which retard crack propagation and improve the fatigue resistance, like shot peening. The cold spray process is shown schematically in figure 1.
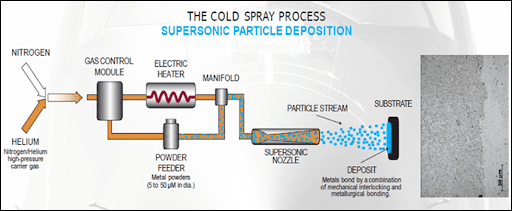
Figure 1. Schematic of a high-pressure cold spray process.
Cold spray is not only used for repair and retrofitting of a structure, but can also be used for corrosion resistance, ballistic resistance, radiation shielding and more. The cold spray process can work with various metals and non-metals such as, aluminum, nickel, stainless, aluminum oxide, steel, titanium, zinc, tungsten copper, nickel chromium, tungsten carbide, and gold.
mattis, pulvinar dapibus leo.
Cold Spray Heat Affected Zone?
As the name suggests, Cold Spray has a different thermal spray temperature than Thermal Spray Coatings and does not directly use heat in its process like welding. Cold spray only uses electricity to heat up the gas that is used to propel the metal particles, otherwise the process does not use heat for its applications. Because of this, cold spray actually doesn’t have a heat affected zone (HAZ). Remember, the HAZ occurs because of the changes in temperature from the welding process. Since cold spray does not affect the heat of the material being worked on, there is no HAZ.
Advantages Of Cold Spray
In addition to not creating heat affected zones, cold spray offers a plethora of advantages for a wide variety of applications and industries.
Here are just a few of the major advantages of cold spray:
- The powder retains its solid form, hence retaining its mechanical properties.
- Maintains a lower substrate surface temperature.
- Less oxidation of the powder and the substrate material.
- Residual stresses are compressive, helping to prevent cracks from forming and growing.
- The resultant cold sprayed deposit can be designed for increased corrosion resistance.
- The coatings repair and strengthen current welds and coatings.
- Extends the product life by up to 50%.
- The impact toughness is increased on welded joints.
Cold spray is providing nearly every major industry a new choice in how they build and repair their products. Cold spray provides all the benefits of traditional welding and then some while also reducing welding major drawbacks, especially HAZ. If you are interested in learning more about cold spray, the process, its benefits and its application then please visit our blog for more informative articles at coldspray.com/article/