Metal Powders and Cold Spray Technology
The metallurgical powder market is poised for a resurgence in 2024 driven by high demand from the aerospace and defense industries. Likewise, other industry giants including marine manufacturers, construction, and the automotive industry are revving their engines, fueled by innovation and a desire for lighter, stronger, and more sustainable materials. These advancements aim to enhance production, maintenance, and repair processes. As technologies like cold spray continue to evolve, the reliance on metal powders is expected to grow not only in 2024 but also beyond!
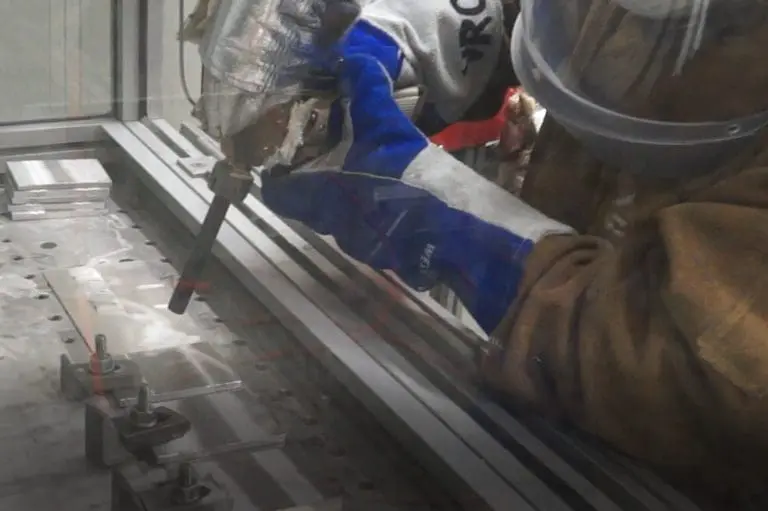
An alternative to thermal spray and welding
For decades, when it came to joining different metals, the options were limited to the searing heat of thermal spraying or the molten dance of welding. Both methods, while effective, have their drawbacks. Thermal spraying can alter the properties of the base metal, while welding can introduce unwanted distortions and residual stresses. But fear not, metal mavens, for a cooler, kinder approach has emerged: cold spray technology.
Imagine a process that bonds metals at supersonic speeds, without melting or distorting them. That’s the magic of cold spray. Finely powdered metals are propelled by a high-pressure gas jet, creating a dense, metallurgical bond upon impact with the target surface. This cold kiss preserves the integrity of the base metal, making it ideal for joining dissimilar materials or those sensitive to heat.
Think of it this way: thermal spraying and welding are like fiery handshakes, leaving their mark on the metals they join. Cold spray, on the other hand, is a quick, clean high-five, preserving the individuality of each metal particle while forging a strong bond. So, the next time you need to join metals, remember, there’s a cooler kid on the block, ready to revolutionize the way we think about metalworking.
How cold spray works
High-pressure cold spray (HPCS) wields metal powders as its ammunition. These powders are propelled to supersonic speeds using a high-pressure gas jet and slam onto metal surfaces, creating super-strong, wear-resistant coating and deposits. Think of corrosion-proof armor for offshore oil rigs, EMI shields for sensitive electronics, and even dimensional restoration for worn-out engine parts – HPCS can do it all and without the need for extreme heat that can warp or weaken the underlying metal, called the Heat Affected Zone (HAZ).
A Global Metal Powder Party in 2024
According to numerous market analysts, the global metal powder market is projected to surge by 7.4% from its current valuation of US$ 9.5 billion in 2022 to reach US$ 19.3 billion by the end of 2032. China is positioned to lead the world in metal powder manufacturing, while the U.S. and North America are expected to be the top consumers of metal powders globally. The U.S. has a strong appetite for metal powders, particularly for additive manufacturing and the steel industry. As the global market for metal powders continues to expand, driven by growth in various emerging technologies, the world’s top economies are actively participating in this dynamic market.¹
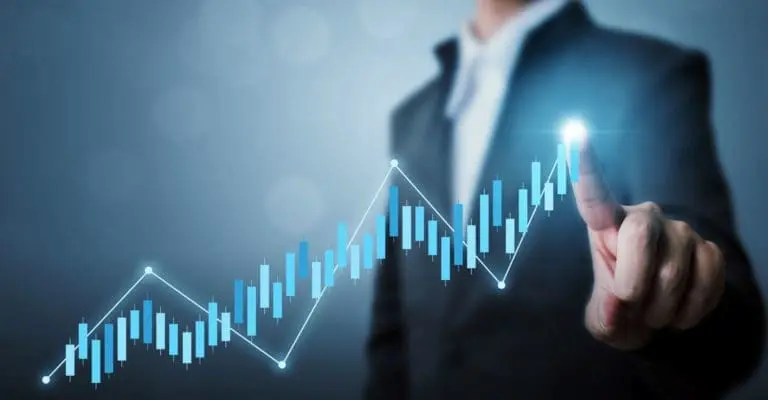
Emerging technologies in metal manufacturing including cold spray technology, 3D printing, and laser cladding can produce new components and repair old ones with comparatively low production costs. The growing demand for numerous metal-fabricated components comes primarily from the aerospace, defense, healthcare, and electronics industries. North America leads the way in this trend, with Asian markets not far behind. While Asia and Eastern markets have traditionally served as the producers of the materials necessary for different metal powder applications, they are rapidly transitioning into consumers of these products as well.² ³
Cold Spray Technology Market in 2024
The global cold spray technology market size was valued at USD 943.5 million in 2022 and is expected to grow at a compound annual growth rate (CAGR) of 6.5% over the forecast period. Many industry analysts have pointed to the demand for cold spray from the medical sector due to cold spray’s ability to administer biocompatible, corrosion-resistant, and high-performance components in the medical industry because of COVID-19. Likewise, analysts also point to increased demand in the defense and aerospace sectors as reliance on lightweight metals increases every day. Recent comments from engineers in the US Navy highlight this fact: “We’ve made some good headway with cold spray in the navy…cold spray gives us a chance to reuse parts we were scrapping; it helps with the material readiness of the fleet. The navy is leaning hard into cold spray.”⁴
Without a doubt, it appears that the aerospace, defense, and healthcare industries are driving most of the demand for cold spray technology.
The Future is Now
While some powder metallurgy applications have been around for centuries, the possibilities with high-pressure cold spray and the metal powder market are mind-blowing. It’s all about having the right materials and technology to unleash the endless potential of this field.
Stay Ahead of the Curve: At ColdSpray.com, we’re passionate about the metal revolution. We believe high-pressure cold spray technology will reshape the future of metallurgy, and we’re here to help you ride the wave.
Sources
1. P. M. Research, “Metal Powder Market,” 2022-2032. [Online]. Available: https://www.persistencemarketresearch.com/market-research/metal-powder-market.asp.
2. [Online]. Available: https://straitsresearch.com/report/powder-metallurgy-market.
3. [Online]. Available: https://www.whatech.com/og/markets-research/materials-chemicals/772992-cold-gas-spray-cgs-coating-industry-booms-2024-2032.
4. [Online]. Available: https://www.janes.com/defence-news/news-detail/surface-navy-2024-us-navy-looks-to-accelerate-cold-spray-applications.