Industries that use cold spray for metal repairs throw around a lot of terms. But what can you do when you’re just starting out in the field? Let’s take a closer look at cold spray terminology for beginners.
According to the cold spray experts at VRC Metal Systems:
“Cold spray, referred to as supersonic particle deposition, is a high-energy solid-state coating and powder consolidation process. Cold spray uses an electrically heated high-pressure carrier gas, like nitrogen or helium, to accelerate metal powders through a supersonic de Laval nozzle above a critical velocity for particle adhesion. The bonding mechanism is a combination of mechanical interlocking and metallurgical bonding from recrystallization at highly strained particle interfaces.”
Let’s look more closely at this cold spray terminology, some additional industry vocabulary, and see if we can speak the same language.
Cold Spray Terminology: The Supplies
Let’s start with the physical supplies needed to apply cold spray terminology to our everyday vocabulary.
Alloy: An alloy is defined as a blend of metals (or other elements) in a solid solution. An excellent example of an alloy is steel. Steel is an alloy containing iron and carbon and often containing other alloying elements.
Carrier Gas: A carrier gas is a gas conveying the metal powder from the powder feeder to the surfacing gun.
- Helium: Helium is a low-density, inert gas used for filling balloons and airships. It is often used in the cold spray process due to its high speed of sound.
- Nitrogen: Like helium, nitrogen is also an inert gas often used as a carrier gas in cold spray. Nitrogen constitutes over 78% of the earth’s atmosphere, yet it will not support life, nor is it combustible. Nitrogen gas is cheap and widely available. However, it cannot achieve the particle speeds that helium can.
De Laval Nozzle: A de Laval nozzle is a nozzle that converts heat energy in the gas to kinetic energy (speed!). A slow, high-temperature gas goes in, and a fast and lower-temperature gas comes out.
Metal Powder: A metal powder is a powder consisting of a single, pure metal. The size for cold spray powders ranges from five to one hundred micrometers in diameter.
- Alloy Powder: An alloy powder is created from a single molten alloy.
- Composite Powder: A composite powder that combines metal particles with two or more individual materials.
Process Gas: The process gas provides the driving force for accelerating the metal powders. The process gas is heated before being blended with the carrier gas and injected into the De Laval nozzle.
Substrate: The substrate is the base material to which the coating is applied.
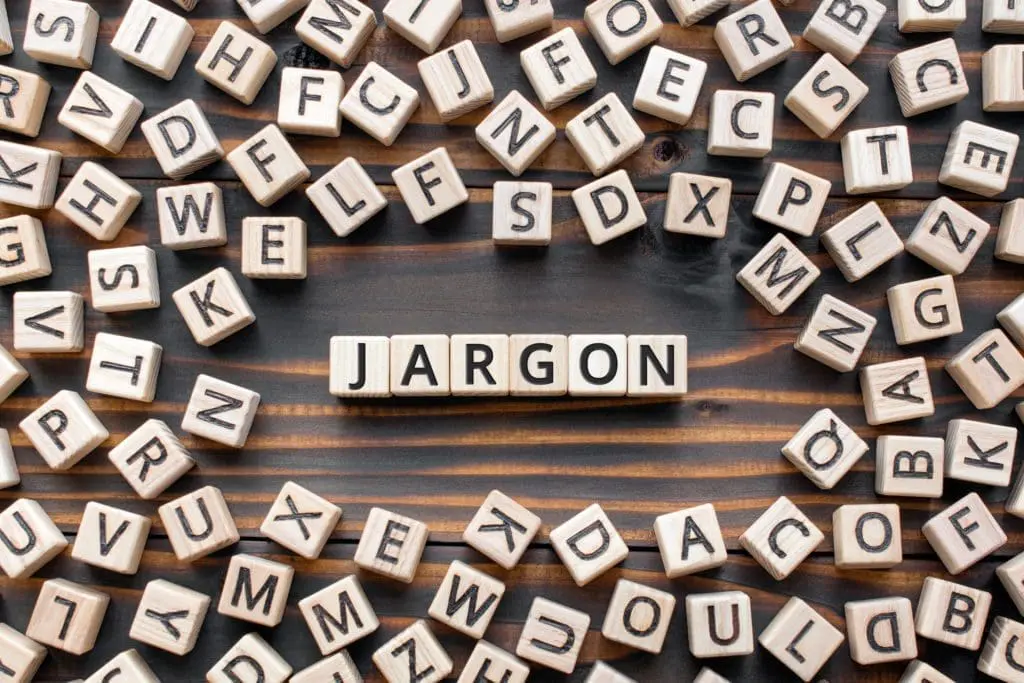
Cold Spray Terminology : The Process
The cold spray process itself is a supersonic particle deposition (SPD) process where the metal powder is accelerated to a super-fast, critical velocity by an inert gas. The resulting bond combines mechanical interlocking and metallurgical bonds from the recrystallization of highly strained particle interfaces.
Here’s a look at some of the cold spray terminology related to the cold spray process:
Critical Velocity: The critical velocity is the speed at which a spray of metal particles transitions from eroding the target surface to coating it instead.
Deposition Rate: The deposition rate refers to the weight of material deposited onto the substrate over a given time. This is usually measured in kilograms/hr (kg/h) or pounds/hr (lb/h).
Elastic Deformation: Elastic deformation occurs in the material below the yield strength and is fully recovered when the load is removed. This is very similar to stretching and releasing a spring.
Feed Rate: The feed rate is when the consumable alloy, metal, or composite powder is “fed through” the cold spray system.
Gas Flow Rate: The gas flow rate is when the gas, usually measured in liters per minute, flows through the cold spray de Laval nozzle.
Mechanical Interlocking: Mechanical interlocking is a mechanical “blending” of the impacting particles and the substrate or previously deposited layers of particles that effectively interlock the layers. This interlocking result can transfer load and resist motion, even if the particles are not metallurgically bonded to the substrate or other particles.
Metallurgical Bond: A metallurgical bond is a type of chemical bond between atoms in a metallic element. Metallic bonding yields specific property characteristics in metals, such as conductivity, ductility, and strength.
Plastic Deformation: Plastic deformation occurs when a metal particle changes shape due to applied stress, pressure, heat, or force. These forces break atomic bonds, and the deformation is permanent.
Recrystallization: Recrystallization is the new grain formation within the metal, often occurring to replace highly deformed (strained) grains. Dynamic recrystallization during the cold spray process can result in nanograin formation, which resists dislocation movement (high strength).
Cold Spray Terminology : The Results
And another great quote from the experts at VRC Metal Systems:
“The cold spray process is applicable to corrosion-resistant coatings…, dimensional restoration and repair …, wear-resistant coatings …, electromagnetic interference (EMI) shielding of components and structures, high strength dissimilar material coatings for unique manufacturing solutions, and field repair of components and systems.”
Let’s break this down now…
Corrosion: Corrosion is the chemical (or the electrochemical) reaction of the substrate with its environment leading to its deterioration. A typical example of electrochemical corrosion is rust.
Electromagnetic Interference (EMI) Shielding: This barrier occurs when using conductive or magnetic materials to form a barrier against electromagnetic fields. Electromagnetic shielding that also blocks radio frequencies is known as RF shielding.
Field Repair: The portability of cold spray systems allows you to take the solution to the component, which is a highly cost-effective way to handle extensive component repairs. Repairing in the field is referred to as a “field repair.”
Wear: Wear refers to the loss of material from a component surface due to some mechanical action such as erosion, abrasion, or fatigue.
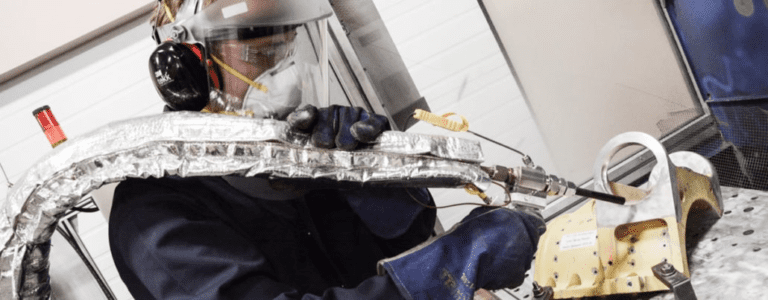
Cold Spray Terminology : The Benefits
Also, some of the benefits of applying cold spray technology include:
Bond Strength: Bond strength refers to the adhesion power between the coating and substrate. For cold spray applications, this is typically >10 kilopounds per square inch (KSI).
Coating Strength: Coating strength is also referred to as spray deposit strength. Typical values achieved exceed 40 ksi.
Porosity: Porosity is also known as the amount of void space in a material, usually below 1% for cold spray coatings.
Oxidation: This is the chemical reaction on the metal’s surface that occurs at high temperatures. Cold spray process temperatures are low enough that no oxidation of metal occurs in the deposition process, leading to minor to no oxide contamination in the coating.
Heat-Affected Zone (HAZ): The HAZ refers to the substrate area that increases in temperature due to the coating application. Cold spray has an inappreciable heat input, thereby minimizing the heat-affected zone on the substrate.
Overspray: Overspray is the small amount of feedstock not deposited on the substrate. Cold spray technology achieves tightly focused particle spray paths, which minimizes the overspray.
Summing It All Up
The cold spray terminology detailed above is a rudimentary list.
To keep on top of all things cold spray and the latest industry news, be sure to check out ColdSpray.com.