Leading market analysts have spoken; cold spray technology has positioned itself for a strong economic future in the years to come. According to recent marketing research, the global cold spray technology market size is anticipated to reach USD 1,559.7 million by 2030 to expand at a compound annual growth rate (CAGR) of 6.5% from 2023 to 2030.¹ The majority of the growth has stemmed from the increase in use of cold spray technology within the aerospace and electronics industries.² Both of these industries have undergone dramatic changes in recent years. What is cold spray technology, and what value does cold spray technology offer to these industries? Why is there such an increase in demand for this new type of technology?
What is Cold Spray Technology?
Cold Spray, also referred to as supersonic particle deposition, is a high-energy solid-state coating and powder consolidation process. It is a process of sending metal particles at supersonic speeds onto a piece of material, thus seamlessly fusing and blending to that material. Cold spray is an efficient method for the application of metals, metal alloys and metal blends for a variety of applications.
Cold spray utilizes electrically heated high-pressure gas, such as air, nitrogen, or helium, to propel the metal powders through a supersonic nozzle above the critical velocity for particle adhesion. The bonding process is a combination of mechanical interlocking and metallurgical bonding. Cold spray can create mixtures of metallic and nonmetallic particles to create a coating or a freestanding structure, giving it the capability to perform corrosion coatings, restoration & repair, electromagnetic shielding and more. The cold spray process can deposit powders such as, aluminum, nickel, stainless steel, titanium, zinc, tungsten copper, nickel chromium, tungsten carbide, gold and more.
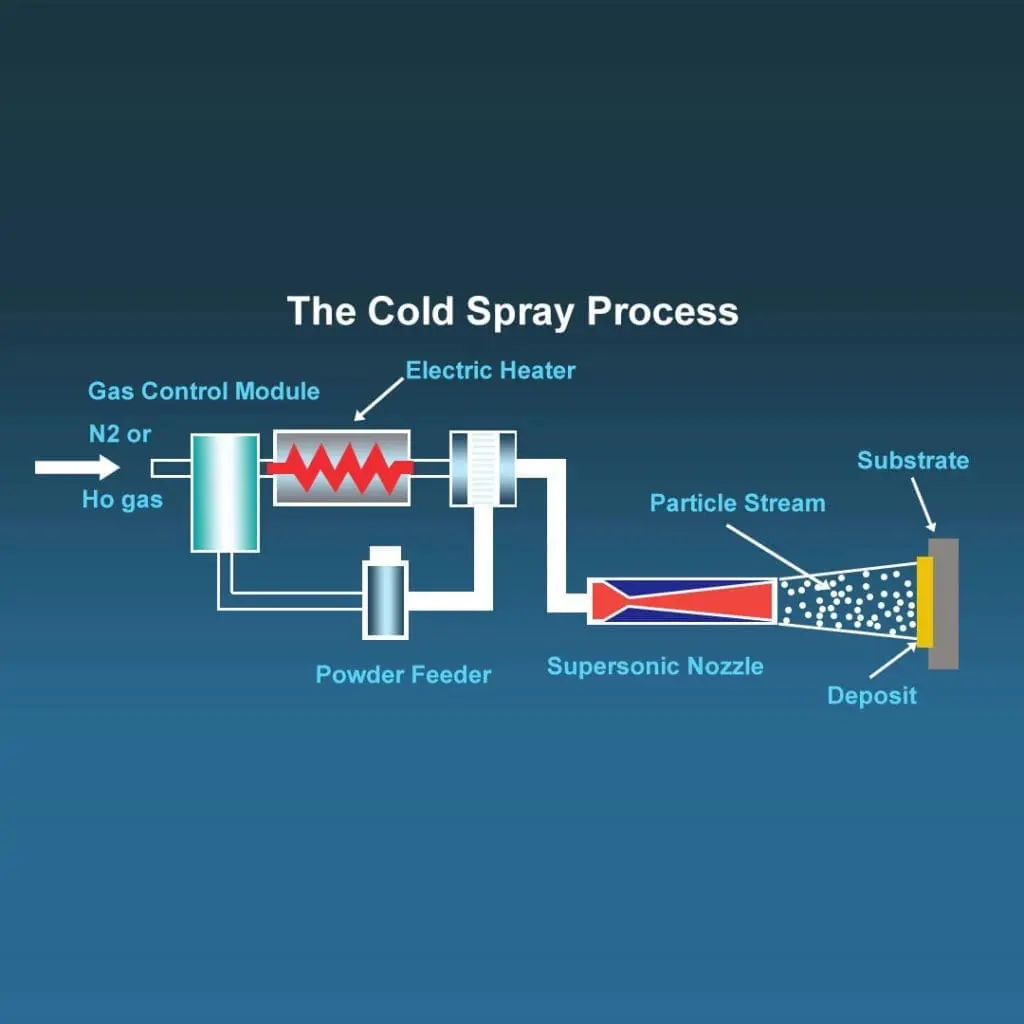
How Cold Spray Technology is changing the Aerospace Industry
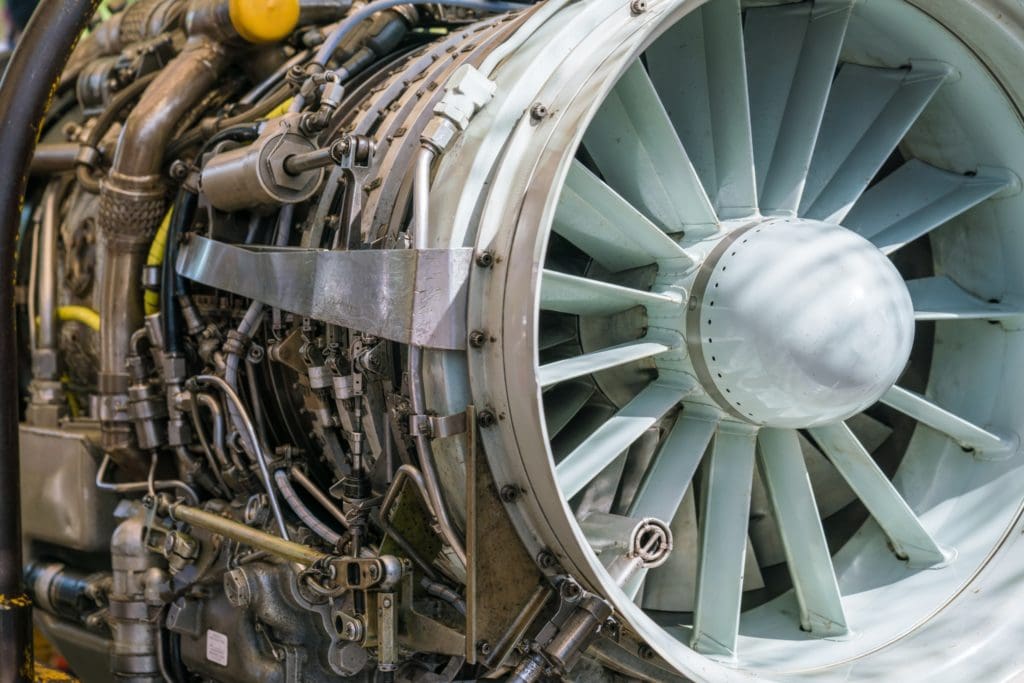
Without a doubt, cold spray technology has shaken up the repair and manufacturing process for the aerospace industry, with quick repairs to aircraft components and efficient manufacturing processes. Cold spray offers improved thermal stability, corrosion resistance, and improved reliability. By minimizing the physical effects when combining different types of metals, cold spray offers repairs to the substrate that outperforms all modern heat welding techniques. By maintaining structural integrity at the heated affected zone without the use of heat, cold spray builds on the existing particles to create a strong bond. Aircraft engineers no longer need to rely on off-site repair of existing components, installing new components altogether, or waiting on costly delivery delays. Cold spray allows repair technicians to make repairs on site, offering repairs to existing components without replacing them.
Cold Spray Technology and the Electrical Industry
Likewise, these benefits extend to electronic components. Cold spray technology can be utilized for coating deposition for electrical components with metals and metal alloys, which improves conductivity and corrosion resistance.³ Multiple electrical components such as circuit boards, electrical contacts, semiconductors, electric motors, and more are coated using cold spray coating technology. As electronic devices decrease in size and increase processing capability, the requirement for improved conductivity becomes paramount. The increased reliance on new electronic technologies is likely driving the majority of this new demand for cold spray technology, as we will see.
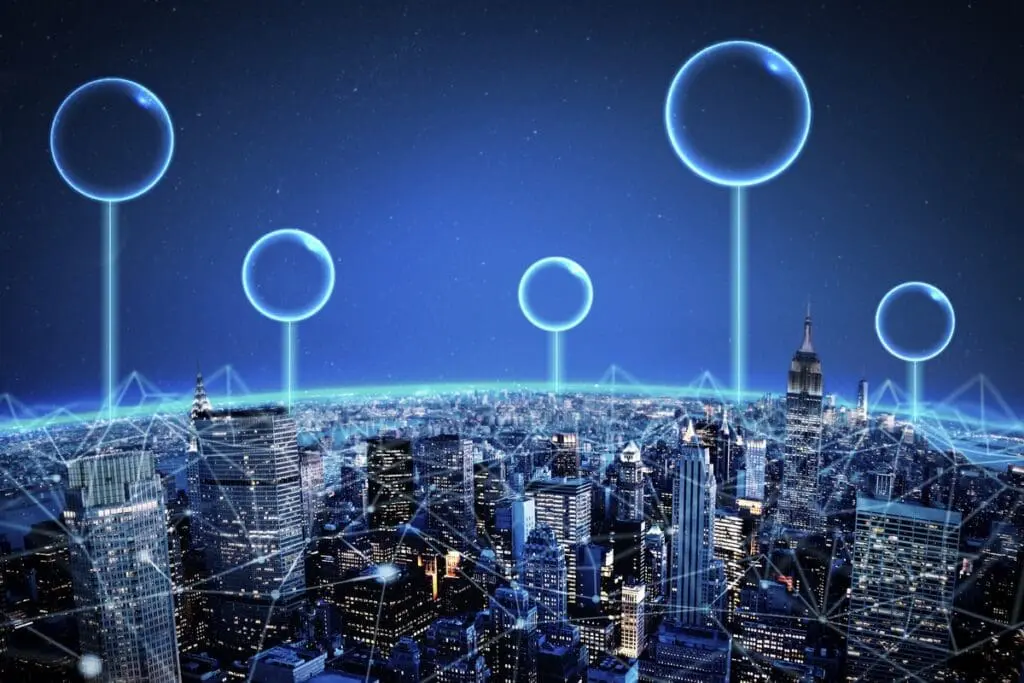
“Internet of Things” Drives New Growth
We see it everywhere: Smart TVs, Smart Phones, Smart Watches, Smart Thermostats, the list goes on. Industry leading experts have noted that flexible electronic components will lead the way as the world becomes more dependent on the “internet of things.” However, the manufacturing process has run into a wall: the post-sintering process allows for oxidation of critical electrical components, increasing the chance of breakdown and poor reliability. Cold spray technology has come to the rescue with the application of resistant coatings to existing components:
The effect of cold spray process parameters on the resultant coatings is comprehensively characterized in terms of microstructure, film thickness, electrical conductivity, linewidth, and adhesion strength. The resulting electrodes show excellent electrical conductivity (6.98 × 105 S m-1), adhesion strength, long-term stability, and flexibility without significant conductivity loss after 1000 bending cycles.⁴
Clearly, as new smart devices require increased electronic capacity this automatically requires improved conductivity and reliability for them to operate properly. The world’s entire business ecosystem is being redesigned and reformatted to rely on these devices, with new markets being created. According to the Groupe Speciale Mobile Association (GSMA), by the end of 2021, approximately 5.3 billion people were subscribed to mobile connections, which represented 67% of the population worldwide. Mobile technologies and services generated approximately $4.5 trillion of economic value added in 2021, which is expected to reach $5 trillion by 2025.⁵ As you can see, the growing electronics industry will drive the demand in the coming years. Cold spray technology will serve as the ultimate bridge between old computer technology and the new vibrant electronic computer ecosystems being built around us everyday.
Summary
In summation, the trajectory of the Cold Spray Technology Market is poised for remarkable growth from 2023 to 2030, driven by its exceptional metallurgical capabilities and multiple applications. This surge is predominantly attributed to its adoption in the aerospace and electronics sectors, where its high-energy solid-state coating process has revolutionized repair, manufacturing, and component reliability. By leveraging supersonic particle deposition, cold spray technology offers seamless fusion, improved thermal stability, corrosion resistance, and enhanced conductivity. Notably, the rapid expansion of the “Internet of Things” has further amplified its demand, necessitating resilient coatings for intricate electrical components.
As the electronics industry continues its unprecedented growth, the role of cold spray technology becomes pivotal in bridging the gap between traditional computing systems and the burgeoning electronic ecosystems that shape our modern world. Simultaneously, as the aerospace industry moves toward sustainability in manufacturing and general operations, new efficient designs require new technologies such as cold spray. Ultimately, both industries will experience growth from the efficiency provided by cold spray technology.
Sources
1. Research and Markets ltd, “Cold Spray Technology Market Size, Share & Trends Analysis Report by Material (Nickel, Copper, Aluminum, Titanium), by Service (Cold Spray Additive Manufacturing), by End-Use, by Region, and Segment Forecasts, 2023 – 2030,” Research and Markets – Market Research Reports – Welcome, accessed August 29, 2023, https://www.researchandmarkets.com/report/cold-spraying-equipment.
2. “Global Cold Spray Technology Market Analysis Report 2023-2030: North America Leads – Flourishing Aerospace & Electronics Industries Drive Demand,” Yahoo! Finance, accessed August 29, 2023, https://finance.yahoo.com/news/global-cold-spray-technology-market-094300503.html.
3. Ibid.
4. D.J. Roach et al., “Cold Spray-Based Rapid and Scalable Production of Printed Flexible Electronics,” Additive Manufacturing, November 2, 2022, https://www.sciencedirect.com/science/article/abs/pii/S2214860422006339.
5. Ibid.