When it comes to undertaking metal repairs, there are a few essential items to consider: materials, reliability, and the best repair method to get to the desired outcome. Cold spray technology is becoming increasingly popular within a range of industries and has become common for repairs.
Read on to see how cold spray technology could help your organization. Whether you perform maintenance in the energy sector, breathe new life into ships and airplanes, or manufacture metal components, your company could benefit!
You can find all of the latest industry information and news on cold spray technology on ColdSpray.com.
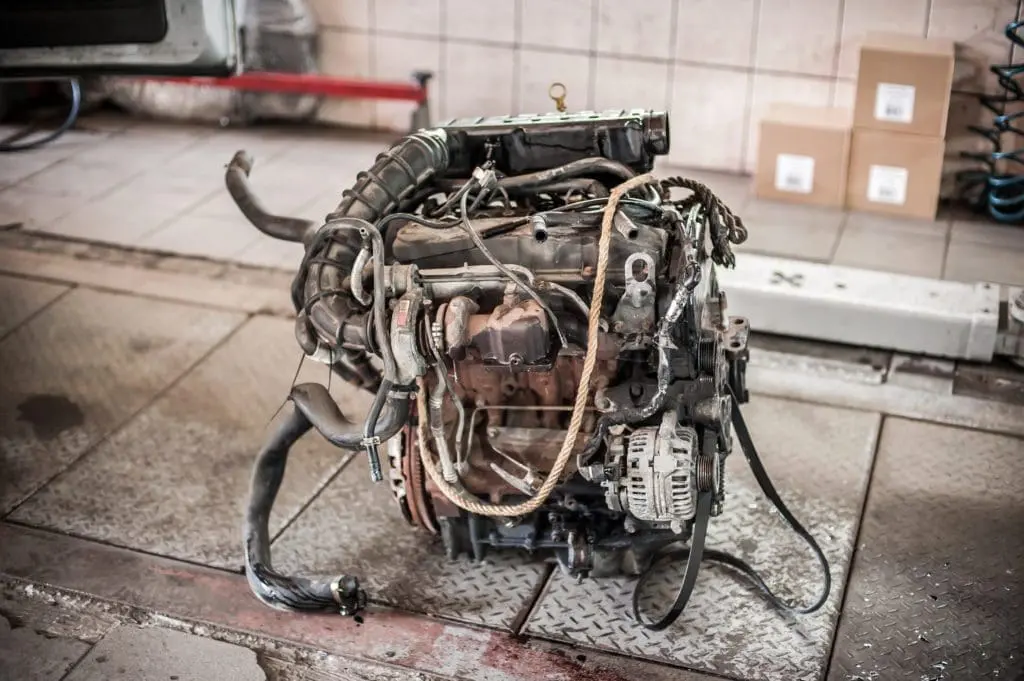
What Is Cold Spray Technology?
Experts first observed cold spray technology in the 1980s at the Institute of Theoretical and Applied Mechanics of the Russian Academy of Sciences. The developers then brought it to the United States in the mid-90s, where research and development began by high-tech entities, such as Sandia National Laboratories and the Army Research Laboratory. Since the mid-90s, it has seen tremendous growth.
Cold spray is one name used to describe a solid-state coating process. In cold spray, a high-speed gas jet accelerates powdered metal particles toward a substrate. Upon impact, the metal particles plastically deform and consolidate, adhering the metallic powder to the substrate.
“Cold spray” is named “cold” due to the low processing temperature. Unlike typical metalworking processes, the spray temperature is usually far lower than the spray material’s melting point.
Cold spray technology has proven suitable for depositing a vast array of materials onto a wide range of substrate material types. It can be instrumental in non-traditional applications which are temperature-sensitive, such as heat-treatable alloys and nanomaterials.
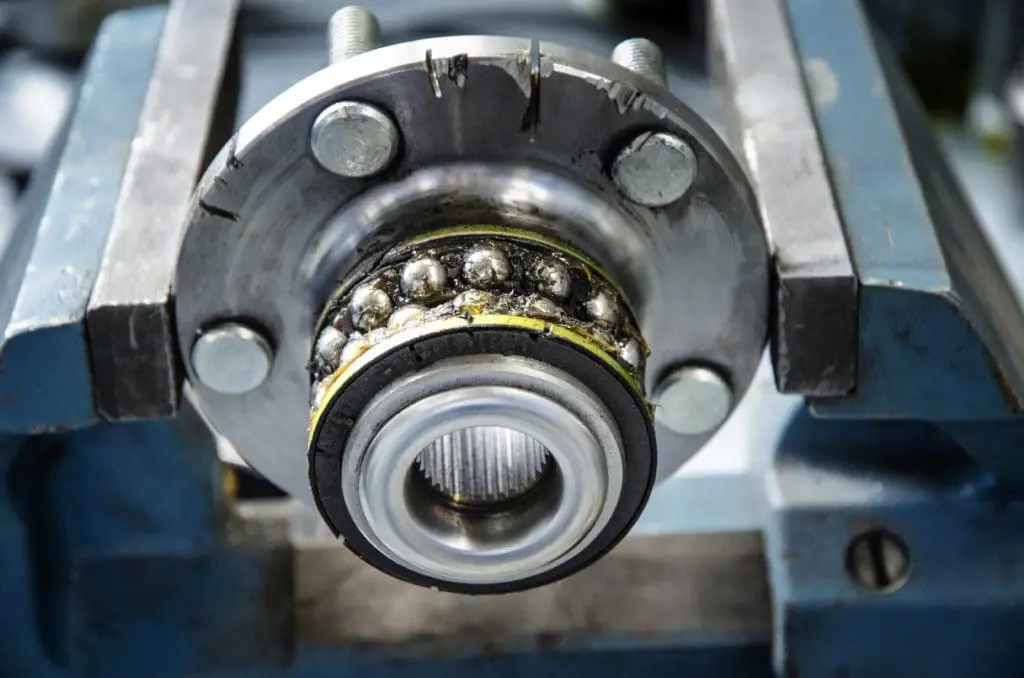
What Are The Advantages Of Cold Spray Technology?
The popularity of cold spray technology continues to rise, with good reason. The technology offers a host of advantages, including:
- Utilizing a low-temperature process compared to other techniques
- No particle or substrate melting
- Reducing or even eliminating grit blasting requirements for substrate adhesion
- Providing low defect coatings
- Minimal oxidation during the process
- Maintaining minimum thickness requirements through multiple repair cycles
- Producing a better surface finish
- Eliminating distortion
- Enabling thicker layers to be created
- Retaining the composition of the initial particles
- Reducing or removing solidification stresses
- Ensuring high hardness
- Requiring minimal cut-back of substrate
- Reducing cooling requirements after the repair
- Allowing pieces to be repaired multiple times during the substrate’s life cycle
Who Is Using Cold Spray Technology?
Cold spray technology is becoming increasingly popular. Some industries making use of this process include:
The Aerospace Industry
When it comes to repairing aircraft, there isn’t room for error. Cold spray technology is prevalent here due to its ability to repair heat-sensitive metals. Aerospace components are not cheap, and repairs are far more economical for businesses – not to mention ticking the box for staying green.
Aircraft Skin Repairs and Access Panel Repairs
Industry standards require the skin of an aircraft be a certain thickness. Using cold spray allows repairs to maintain this without compromising its integrity.
Many of the alloys used in the aerospace industry exhibit high levels of heat sensitivity. Aluminum, magnesium, and titanium are the most common alloys used. They are all sensitive to oxidation and to the effects of heating and cooling too quickly.
The lower temperatures required for the cold spray process make it a perfect fit for aerospace engineering. There is no need to cool down the metal afterward, and the initial temperatures are not high enough to weaken the alloy.
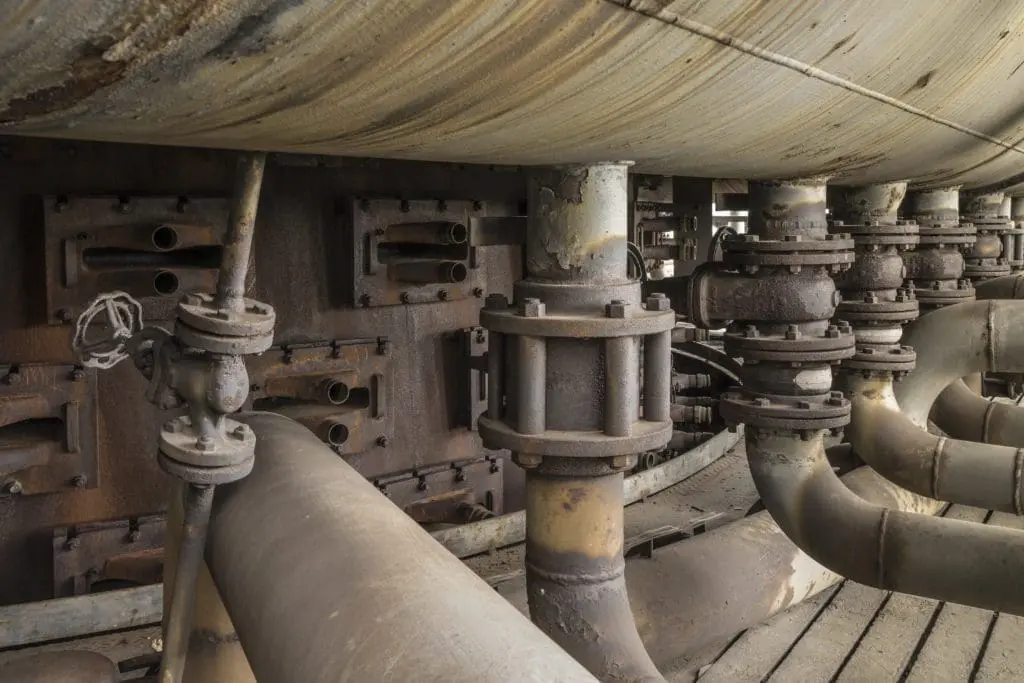
Liquid Handling Systems
If you are involved in repairing machinery and liquid pipelines, cold spray could also help. Leak repairs to active pipelines are possible with this technology, as are repairs to energized systems, whether they are tanks, pipes, fittings, or valves.
The low temperatures required by cold spray allow the substrate’s structural integrity to remain intact. Therefore, in the case of corrosion or damage to a pipe, you can repair the problem without causing further weakness or damage – a critical element if you’re working on an active pipeline. Cold spray technology also allows the targeting of repairs to only the affected area. This differs from welding, which requires a total overhaul of the pipe or system.
Also, the application of cold spray deposits can enhance a substrate over time and repeated application. Repairs can incorporate ceramics and carbides, and this helps to provide significant wear benefits.
Cold spray technology allows for hard-to-remove components in a machine to be repaired, rather than replaced, without concerns for their long-term structural integrity.
Those other existing repair actions, such as welding, extend the length of the repair project and cause a not insignificant inconvenience. Repairing the broken component, in situ and to a higher standard, is the “holy grail” for these customers and is a substantial factor in why cold spray is gaining popularity.
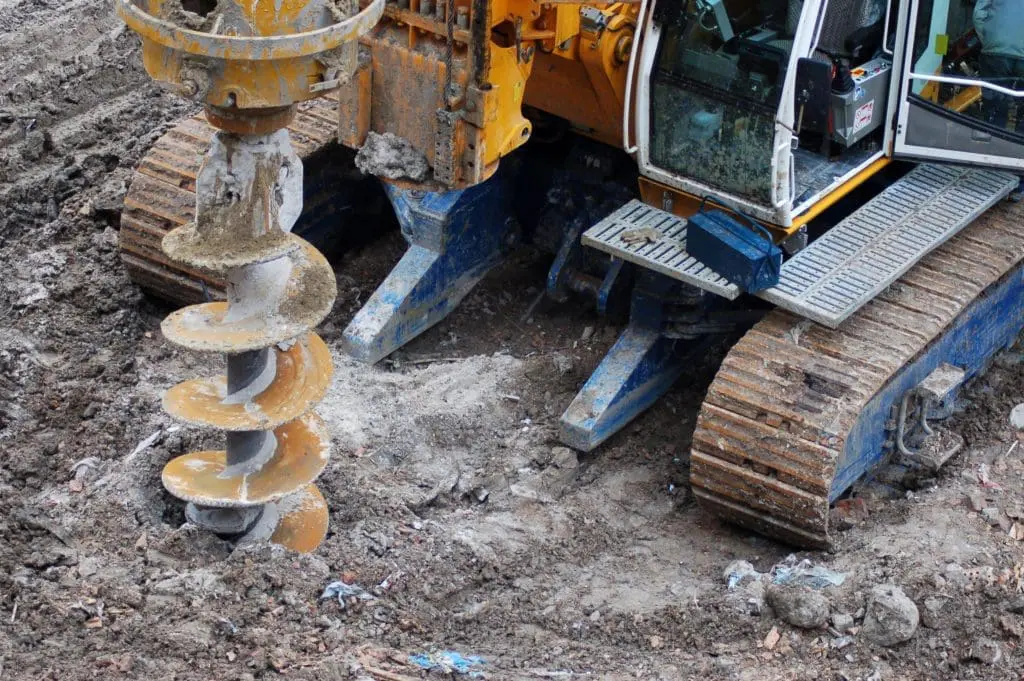
Large Equipment Repairs
Cold spray can also be invaluable when it comes to large equipment repairs. Why? Mainly for the reasons this blog post mentioned earlier — cold spray technology allows for targeted repairs to the areas of damage instead of requiring entire components to be removed and replaced.
Stay Up To Date!
Staying up to date with the latest industrial advances is crucial. It keeps you at the front of your industry and ensures that your business runs in the most efficient manner. Plus, it will get your team excited about their careers and inspired by watching the impossible become possible!
You can find all of the latest industry information and news on cold spray technology on ColdSpray.com.